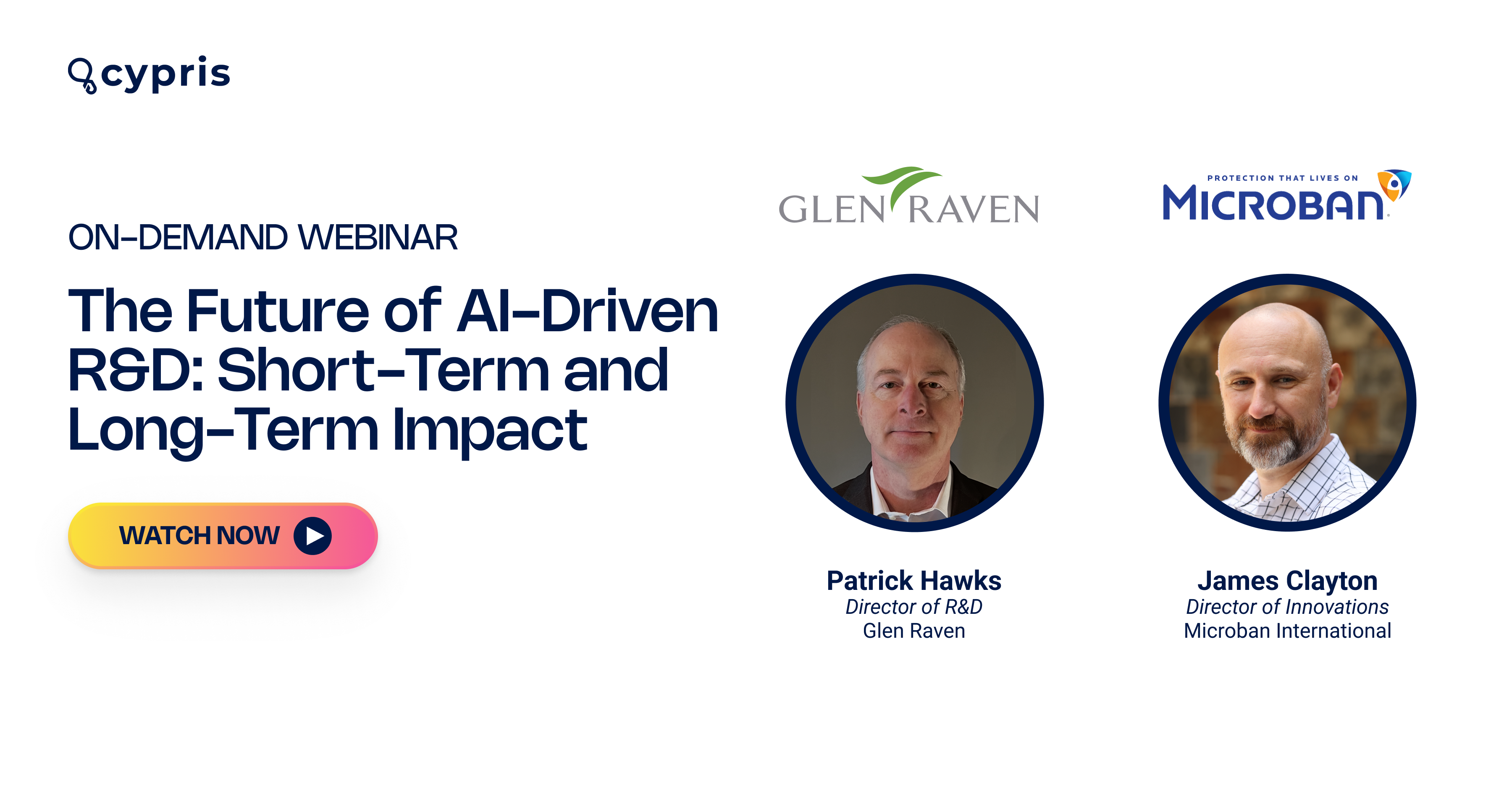
Webinar: The Future of AI-Driven R&D: Short-Term and Long-Term Impact
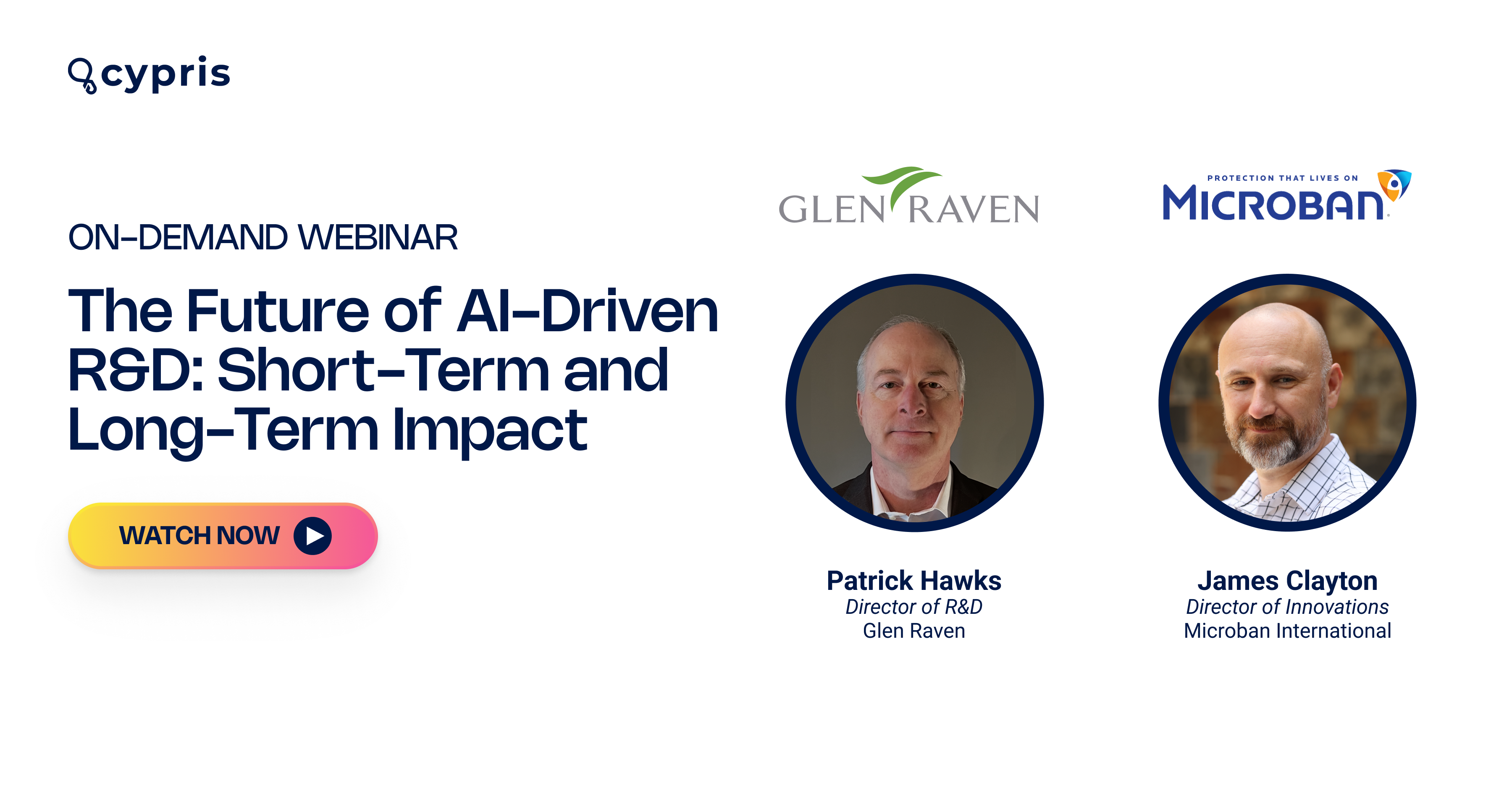
Today, the need for society to adopt sustainable practices is increasingly urgent, particularly in chemical manufacturing, which is responsible for greenhouse gas emissions, toxic waste, increased water and energy consumption, and inefficient raw material use. Consequently, the market for sustainable chemical manufacturing has surged to $10 billion and continues to expand as the focus on sustainability intensifies. Leading this charge are three innovative approaches: mechanochemistry, green synthesis, and microflow chemistry. Mechanochemistry, which induces chemical reactions through mechanical energy, accelerates reactions and conserves energy compared to traditional solvent-based methods, while reducing reaction mass and potentially increasing product yield by avoiding solvents. Green synthesis aims to minimize the use and generation of hazardous substances, thereby reducing environmental impact and enhancing sustainability, with notable examples including the synthesis of spirooxindole derivatives using heterogeneous catalysis and metal-organic framework (MOF) catalysts. Microflow chemistry, or continuous flow chemistry, involves reactions in microreactors that allow precise control over reaction conditions, enhancing safety, scalability, and efficiency. The integration of these three approaches—mechanochemistry, green synthesis, and microflow chemistry—represents a significant advancement in sustainable chemical manufacturing, addressing critical challenges from waste reduction to energy savings and paving the way for a more sustainable industry.
Mechanochemistry: Mechanochemistry accelerates reactions and reduces solvent use, advancing sustainability in chemical manufacturing.
Mechanochemistry, a process in which chemical synthesis is induced by external mechanical energy, has gained attention in chemical manufacturing due to its sustainable nature. This method allows reactions to occur more quickly and saves energy compared to traditional solvent-based chemistry. Mechanochemistry also offers cost and time efficiency by eliminating the need for solvents, thereby reducing 90% of the reaction mass, and potentially increasing product yield under optimal conditions.
The disposal of plastics, which are non-biodegradable and create significant pollution, is a growing concern for the health and longevity of the planet. Recently, research has focused on using mechanochemistry to control the degradation of polymers found in plastics. Researchers have discovered that the previously separate fields of polymer and trituration mechanochemistry can converge, enabling the degradation of polymers through milling and grinding. This breakthrough holds the potential to significantly mitigate global warming.
Green Synthesis: Green synthesis reduces hazards and waste with efficient methods like heterogeneous and MOF catalysts.
Green synthesis involves creating chemical products and processes that minimize the use and production of hazardous substances, aiming to reduce environmental impact and enhance sustainability in chemical manufacturing. This approach not only benefits the environment but also protects the health and safety of chemical workers and consumers, while reducing costs associated with waste disposal and raw material use.
Spirooxindole has been a focus in the green synthesis field due to its broad benefits in medicine as well as agriculture because of it being a unique compound because of the high reactivity of the carbonyl group located at the 3-position of isatin. Various green synthesis methods have been used for creating spirooxindole derivatives. Various green synthesis methods have been developed for creating spirooxindole derivatives, with one promising approach being the use of heterogeneous catalysts. These catalysts, which are in different phases from the reactants and products, allow for effortless separation, minimizing waste, shortening processing time, and conserving energy.
Another promising method in green synthesis is the use of metal-organic framework (MOF) catalysts. MOFs are attractive due to their high surface area, large porosity, multiple catalytic sites, and highly tunable composition and structure. Studies have shown that MOF catalysts can achieve high yields of 95%-99% and short reaction times. For example, Mirhosseini-Eshkevari et al. (2019) synthesized a zirconium metal-organic framework (Zr MOF) called TEDA/IMIZ-BAIL@UiO-66 using benzene dicarboxylic acid as the organic linker. This framework served as a heterogeneous catalyst in the synthesis of spirooxindole derivatives, with the BAIL@UiO-66 catalyst acting as a Brønsted acid to enhance the electrophilicity of the carbonyl group in isatin and promote nucleophilic attack. This catalyst can be reused in other reactions with minimal reduction in yield, demonstrating its potential as a promising alternative to non-renewable processes.
Microflow Chemistry: Microflow chemistry boosts efficiency and sustainability with precise control and effective processing of renewable resources and waste.
Microflow chemistry, also known as continuous flow chemistry or microfluidic chemistry, is highly regarded for its efficiency, safety, and sustainability in chemical manufacturing. This approach involves chemical reactions occurring in microreactors, which allow for precise control over reaction conditions, thereby enhancing safety, scalability, and efficiency. Microflow chemistry is utilized in various fields, including environmental science, fine chemicals, materials science, and pharmaceuticals.
Recently, microflow chemistry has proven sustainable not only due to its efficient process but also because of its applications. It is now central to green catalytic engineering for processing renewable resources. For instance, microflow chemistry is used to process lignocellulosic biomass into fuels and chemicals. Lignocellulose, found in the microfibrils of plant cell walls and composed mainly of polysaccharides and lignins, has been extensively studied for this purpose. Microflow chemistry is highly favored for this process due to its enhanced product yield and selectivity.
Furthermore, microflow chemistry improves sustainability in on-site chemical manufacturing. Biomass, which contains a significant amount of water, requires considerable energy for transportation to refineries, making onsite processing essential. This is also true for food waste, which has a short shelf life and is produced in large quantities. Even plastic waste, despite its longevity and low water content, is widespread in landfills and ecosystems, necessitating onsite processing in remote and offshore areas. Microflow chemistry offers better economic viability and higher energy efficiency, supporting sustainable onsite manufacturing.
The crucial shift towards sustainable practices in chemical manufacturing is driven by the environmental and societal challenges posed by traditional methods. Innovations like mechanochemistry, green synthesis, and microflow chemistry are at the forefront of this transformation. Mechanochemistry accelerates reactions while minimizing solvent use, promising reduced energy consumption and waste generation. Green synthesis techniques, utilizing heterogeneous catalysis and metal-organic frameworks, provide efficient, low-impact pathways to valuable compounds like spirooxindoles, essential in medicine and agriculture. Microflow chemistry, with its precision in controlling reaction conditions, enhances safety and efficiency, especially in processing renewable biomass and managing onsite waste such as food and plastic. Together, these approaches not only reduce environmental impacts, including greenhouse gas emissions and toxic waste, but also promote a more resilient and sustainable chemical industry, ready to meet future challenges.